Introduction
The petroleum industry technique known as hydraulic fracturing or, more informally, "hydrofracking" and "fracking," is a widely used and effective method of enhancing the recovery of oil and gas from deposits that were previously too costly to develop. Its use, especially in combination with horizontal drilling, has transformed the economy of the U.S. petroleum industry since its rapid adoption over the last several decades. Hydraulic fracturing has also recently been a topic of widespread media interest and scientific research. Much of what is reported in the media focuses on possible health and environmental risks associated with the practice. Although no case or claim of contamination from hydraulic fracturing has been reported in Indiana (McDivitt, 2009; Herschel McDivitt, Ind. Division of Oil and Gas, personal communication, 2013), we should watch for signs of possible contamination that may have gone unrecognized or that could affect the quality of groundwater in the future. If new research reveals that significant adverse health and environmental conditions or risks do exist, a reasoned response to the problem should be implemented (Saba, 2013).
Here, we offer a brief explanation of the process of hydraulic fracturing and its importance as a technique for recovering oil or natural gas from reservoirs once thought to be difficult or impossible to develop economically. The health and environmental consequences that may be associated with hydraulic fracturing operations are also addressed. Broader issues—land usage, regional groundwater conservation, economic implications of oil development versus alternate fuel options, and societal lifestyle choices are beyond the scope of this paper.
The Hydraulic Fracturing Process
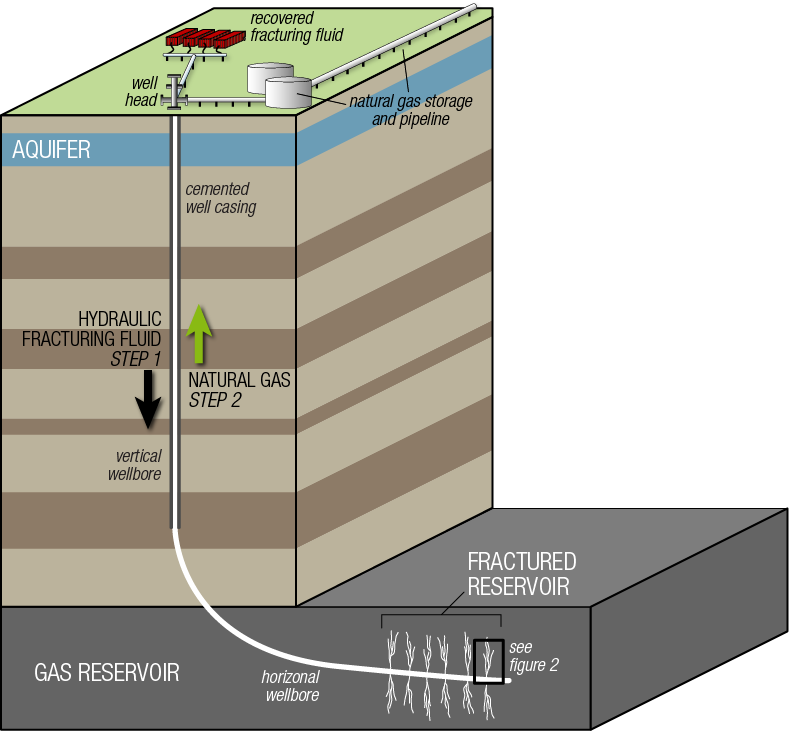
Figure 1.
Schematic illustration of a hydraulic fracturing operation and horizontal well.
Hydraulic fracturing involves injecting a mixture of water, sand or sand-sized particles, and chemical additives into a subsurface petroleum reservoir at high pressure (fig. 1). Injection creates and holds open small fractures, about as wide as one or two grains of sand, in the vicinity of the well. These propped-open fractures serve as fluid pathways in the reservoir, permitting the fluids in the reservoir to flow more readily to the wellbore (fig. 2). Injection pressures are high enough to create small interconnected cracks in the rock. The sand props open these cracks, and the additives reduce friction, control bacterial growth, and inhibit corrosion, all of which improve fluid flow from the fractured reservoir rock (FracFocus, 2013). The additives typically include from three to twelve chemicals, used in concentrations making up 0.5 to 2 percent of the total injected liquids, the remainder being water.
Although the sudden release of pressure when a reservoir rock fractures can be quite powerful, it is highly controlled; this assures that the fracturing remains largely within the reservoir formation. Hydrofracking is an expensive process, and it is to the advantage of the operator to limit the fracturing to only potentially productive rock strata. This is accomplished by careful design and engineering of the fracturing process.
Another practice that has grown in the past 10 to 15 years in the United States is "staged fracturing." Instead of fracturing the entire length of an oil- or gas-bearing rock in a single operation, the treatment interval is divided into sections that are each fractured separately. This concentrates more pressure on each fracture interval.
Conventional and Unconventional Wells
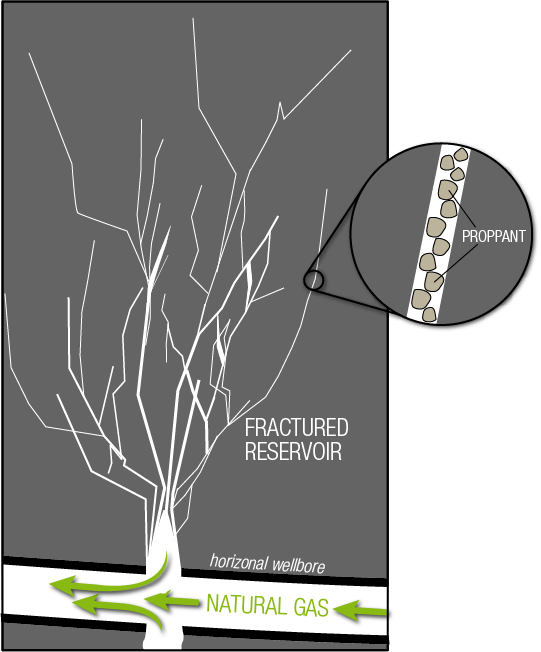
Figure 2.
Schematic illustration of fractures in a natural-gas-bearing shale reservoir. The proppant (usually sand) holds
the fractures open to allow natural gas to flow from the reservoir to the wellbore. The fracture density is
likely denser than what is shown. Illustration not to scale.
Petroleum accumulates and resides in porous reservoirs within the Earth. Impervious layers of rock seal or trap the fluids within the reservoir and prevent their escape to the surface. Petroleum will remain trapped in a reservoir until the seal is breached, either naturally by tectonic forces or slow leakage, or through human activities such as drilling. In a conventional oil or gas well, the drilled hole is a conduit that allows petroleum in the reservoir to flow or be pumped to the Earth's surface. These wells are called "conventional" because they recovered oil and gas using the standard drilling practices of the time. Those standard practices were effective for most reservoirs that had sufficiently large pore spaces (porosity) and unblocked flow pathways (permeability) between the reservoir rock grains.
Historically, conventional reservoirs were drilled and exploited first, because they were the easiest and most economical to develop. As those petroleum reserves were exhausted, however, the industry increasingly turned its attention to rocks that were less permeable and more difficult and costly to exploit. These "unconventional" reservoirs—shale beds, "tight" or low-permeability sands and siltstones, and, low-permeability carbonate reservoirs)—require advanced technologies to produce enough oil or gas to be economically viable. Hydraulic fracturing is an effective method to increase the production from these unconventional reservoirs.
Hydraulic fracturing is often used in conjunction with horizontal drilling, which can greatly increase the amount of oil and gas recovered. Horizontal drilling involves deviating a vertical well bore along a curved path to intersect a reservoir in a near-horizontal plane. Throughout the drilling process, the horizontal bore extends within the petroleum-bearing rock strata, which results in a greater exposure of the well bore to recoverable petroleum (Helms, 2008). Both hydraulic fracturing and horizontal drilling technologies were already used independently in conventional reservoirs. Although hydraulic fracturing techniques have been employed widely since the late 1940s, and horizontal drilling was invented in 1929, they only became commercially viable in the early 1980s when they began being used together, initiating an exploration and development bonanza in the United States.
Hydraulic Fracturing in the United States and in Indiana
In the United States, reservoirs that undergo hydraulic fracturing typically occur at depths of 6,000 to 10,000 feet (FracFocus, 2013). In Indiana, reservoirs that have been hydraulically stimulated are at depths from 200 to 4,000 feet, averaging about 1,500 ft. The average fracturing interval depth is skewed to the shallow side by wells targeting coal-bed methane production. The majority of coal-bed methane beds in Indiana are shallower than 600 feet deep. Given their presumed proximity to possible subsurface aquifers, they are governed by special rules established by the state legislature that call for greater control of drilling, well treatments, and water management (http://www.in.gov/legislative/iac/20110727-IR-312110432ERA.xml.html). These rules are administered by the Indiana Department of Natural Resources Division of Oil and Gas. Also, fractures created or enhanced by hydraulic fracturing relatively more constrained within shallow horizons because their structural stress regimes favor development of horizontal rather than vertical fractures (see section entitled Potential Contamination of Subsurface Aquifers, later in this report).
Around 2001, when coal-bed methane fracturing began to be used in Indiana, common fracture treatments employed approximately 10,500 to 12,000 gallons of frac fluid plus 6,000 lbs. of sand. By the mid-2000s, most coal-bed methane fracturing used from 39,000 to 42,000 gallons of frac fluid and 8,700 to 10,200 pounds of sand. For other types of wells, however, the amounts sometimes exceeded 60,000 gallons of frac fluid and 60,000 pounds of sand. Recently, Rex Energy filed a hydraulic fracturing report for the T.C. Cooper H-1 well in Gibson County (IDNR DOG permit #54713; IGWS PDMS ID #166489), that showed a fracture stimulation in April 2013 totaling 2.1 million gallons of fluids. The public can view this report at (http://b3.caspio.com/dp.asp?AppKey=311a10005064ebffbb014705b4ab%20&IGS_ID=166489).
After fracturing, petroleum and some of the injected fluids are recovered from the well at ground surface during a period known as "flowback." Ideally, all the injected sand or a similar proppant (material that props open the cracks), would remain lodged in the subsurface fractures when the injection pressure is decreased, but some proppant, along with some of the injected water and additives, flow back out of the well after the treatment. During flowback, it is important to clean up the well and flush the excess proppant that may not have completely entered the formation or that accumulated in the bottom of the well. The amount of injected fluid typically recovered after hydraulic fracturing varies considerably throughout the country, ranging from 5 to 50 percent (King, 2012). The rest of the fracturing fluid and additives remains in the reservoir where it is trapped in small pores or as adsorbed fluids. Water that exists naturally in the pores of the reservoir along with oil and gas is also part of the fluid produced during the flowback period.
In the northeastern United States, where the Marcellus and Utica shales are being developed, the amount of water used to fracture wells ranges from six to ten million gallons per well (McDivitt, 2013; FracFocus, 2013). By comparison, the volumes of frac fluid typically used in Indiana are significantly less.
Year | Minimum for Single Treatment | Mean Average Single Treatment | Maximum Single Treatment | Total for Hydraulically Fractured Wells |
---|---|---|---|---|
2011 | 1,000 | 34,522 | 354,706 | 1,352,932 |
2012 | 250 | 160,835 | 602,616 | 10,769,973 |
2013 | 840 | 202,813 | 2,095,128 | 19,667,515 |
Table 1. Volumes of frac fluid (gallons) used in hydraulic fracturing treatments in Indiana for the years 2011-2013. (Herschel McDivitt, written communication, 2014)
The records of the Indiana Department of Natural Resources reflect that, for 2012, a collective total of 10.7 million gallons was used for fracture stimulation. In 2013 (through Nov. 1), a total of 13.2 million gallons was recorded. In the seven years previous to 2013, total frac volumes each year totaled less than 1 million gallons (Herschel McDivitt, Ind. Division of Oil and Gas, personal communication, 2013).
The Importance of Hydraulic Fracturing
Hydraulic fracturing, first used commercially in the United States in 1949 (Montgomery and Smith, 2010), is an important well-completion technique that accounts for the significant increase of oil and gas recovered in the nation and the state; it is credited with the marked increase of U.S. petroleum reserves in otherwise uneconomic reservoirs. The American Oil and Gas Reporter (Fisher, 2010) estimates that as many as 90 percent of all gas wells in the United States have been fractured, and 30 percent of oil and natural gas reserves are recoverable because of hydraulic fracturing. Wells that depend on hydraulic fracturing to perform effectively will play an increasingly important role in the nation's energy future, even as we transition to a greater reliance on alternative energy sources. The National Petroleum Council (2011) reported that hydraulic fracturing accounted for more than 43 percent of total U.S. oil production and 67 percent of natural gas production at that time.
Hydraulic fracturing has reversed the dependence of the United States on imported energy. For many years our dependence on foreign oil, often from troubled countries with unstable governments, increased every year. Hydraulic fracturing also has shifted exploration focus from offshore (essentially, Texas and Louisiana) to onshore basins that have large nearby energy demands, for example, the Marcellus shale and nearby population centers in the northeast.
Environmental and Health Concerns
Composition of Fracturing Materials
Any time that oil and gas wells are drilled, there is the risk of environmental contamination. Such risks include, but are not limited to, ground spills of drilling or fracking materials, spills during transport to the well, accidental compromise of the well bore, failure to isolate the well's mud circulation system, failure of hardware installed in the hole, failure when treating the well, and processing and transporting waste fluids to a waste disposal well.
Aside from the risks associated with any oil and gas well operation, there are many concerns about fracking fluids. Industry service companies were reluctant to reveal the composition of fracking fluids, citing their need to protect proprietary formulas. However, a recent study by the U.S. House of Representatives entitled "Chemicals Use in Hydraulic Fracturing" (2011), leaves little doubt that some hazardous, and even carcinogenic, materials may be used in some fracturing fluids. The report was based on replies from the 14 leading oil and gas service companies in response to a request for information by the House. More than 650 products used in hydraulic fracturing from 2005 through 2009 contained one or more of 29 chemicals that are either known or possible human carcinogens. Since these concerns were first raised six to eight years ago, most state oil and gas regulatory agencies, including the Indiana Division of Oil and Gas, have required oil and gas operators to report detailed information about various additives and their potential health risks. In Indiana, operators are required to supply safety data sheets that are prepared by the chemical products manufacturers; these include information about the various ingredients in products and any health, safety, or environmental precautions that must be taken when handling the products. A list of products used in hydraulic fracturing treatments in Indiana is available on the Division of Oil and Gas website (http://www.in.gov/dnr/dnroil/6599.htm). The greatest risk is when these components are handled at the surface: transporting to the well site, mixing the components prior to injection, and placing the waste water in storage tanks at flow-back. However, the use of many of these materials is on the decline, as the industry discovers alternate additives that can substitute for the hazardous components (King, 2012).
In light of public concern about the dangers of hydraulic fracturing, a number of governmental, professional society, and industry organizations are studying its environmental effects. To date, a rigorous and comprehensive comparison of the various chemical products used in the fracturing process does not exist; however, industry service companies are actively pursuing research to create better recipes for fracturing fluids that would reduce or eliminate hazardous components. Among other processes being investigated are waterless fracturing and recycling recovered frac water for use in subsequent fracturing jobs. The U.S. Environmental Protection Agency is currently evaluating fracking chemicals and is scheduled to release a report by late 2014 (USEPA, 2013).
Acceptable or Unacceptable Risk
Because hazardous materials are currently being injected into subsurface petroleum reservoirs (U.S. House of Representatives, 2011), a major question must be addressed: Is this practice and the risks it involves acceptable? In the United States, it is assumed that a degree of acceptable risk is necessary in any industrial practice, but that it should be balanced against the purported beneficial gain. The benefits of using hydraulic fracturing chemicals include increased oil independence and cheaper prices. We outline the risks in the following sections.
Potential Contamination of Subsurface Aquifers
The possibility of contaminating groundwater and water wells by hydraulic fracturing is a major consideration because of its potential immediate impact as well as its long-lasting consequences. Aquifer contamination could occur if the process of hydraulically fracturing a reservoir created conduits in the subsurface that extended from the reservoir to an aquifer. In such a scenario, frac fluid is forced under pressure into a potable water aquifer, thereby contaminating the aquifer and likely rendering its water unfit to drink. Although this chain of events is possible, the pressure regime of a fracture-treated reservoir makes this scenario unlikely. When a well is hydraulically fractured, frac materials are injected under considerable pressure into a reservoir until the reservoir formation fractures (a process that can last a few days). When the treatment is concluded, the pressure balance is immediately reversed and fluids flow back from the reservoir toward the fractured wellbore. For the remainder of the well's life (excluding periodic re-fracturing treatments every few years), the reservoir pressure maintains the flow toward the borehole, meaning that frac materials will not flow away from the borehole toward isolated aquifers in other areas or toward shallower parts of the stratigraphic column.
Whether such a direct transfer of fracturing fluids from a petroleum reservoir to an aquifer has ever been documented in the United States is a matter of some contention in the literature (NGWA, 2011; AASG, 2012; King, 2012). However, even if a number of cases of contamination are recognized in the future, they would still be considered rare, given the tens of thousands of hydraulically fractured wells and the paucity of reported contamination events. Herschel McDivitt, director of the Indiana Division of Oil and Gas, stated, "There have been no instances where the Division of Oil and Gas has verified that harm to groundwater has ever been found to be the result of hydraulic fracturing in Indiana. In fact, we are unaware of any allegation that hydraulic fracturing may be the cause of or may have been a contributing factor to an adverse impact to groundwater in Indiana."
Despite the empirical suggestion that hydraulically fractured reservoirs have not contaminated aquifers in Indiana, we must consider the various ways that such contamination could occur and what steps should be taken to prevent this from happening. For fracturing fluids to contaminate an aquifer, a pathway of fluid communication must exist between the injected petroleum-bearing formation and the aquifer. To evaluate this risk, we must consider several possibilities.
Direct Communication through Fractures
Studies of hydraulic fracture patterns show that fractures do not generally extend for long distances, either horizontally or vertically (Fisher and Warpinski, 2011). Fracturing the rock "out of zone" (vertically or horizontally far from the reservoir) is not in the financial or technical interest of the operator. Petroleum engineers take great care to design fracturing programs that maximize fracturing within and very near the reservoir. The propagation of fractures vertically has been studied extensively in several thousand fracturing operations in the Barnett (Texas), Eagle Ford (Texas), Marcellus (Pennsylvania), and Woodford (Oklahoma) shale intervals. The maximum reported height of an upward-propagating fracture is about 1,900 feet, and the typical distance between the top of a fracture zone and the deepest aquifer is between 3,800 and 7,500 feet (Fisher, 2010; Fisher and Warpinski, 2011; Davies and others, 2012). Warpinski (2011) concluded, "Fracture heights of several hundred feet are common, and they may occasionally exceed 1,000 feet in a few deep reservoirs. However, there has never been an observed case of a hydraulic fracture propagating thousands of feet vertically to intersect an aquifer. In shale projects where large fluid volumes are injected, the thousands of diagnostic measurements have consistently shown that fractures remain thousands of feet deeper than the aquifers."
In Indiana, conditions are quite a bit different because the target formations are much shallower than in the above-mentioned oil and gas regions. While fracturing at depths less than 2,000 feet might at first seem more likely to increase the chance of opening a fracture-path through hydraulically-enhanced fractures, structural properties of relatively shallow rocks, including petroleum reservoirs and aquifers, actually propagate overwhelmingly along horizontal planes because vertical stresses in the overlying rock column are weaker than the maximum horizontal stress in the formation (Fisher and Warpinski, 2011). Therefore, when a formation is hydraulically fractured, the fractures are unlikely to break into adjacent strata and make their way into unconnected aquifers.
Casing Breaches
When a petroleum well, whether hydraulically fractured or not, is ready to begin producing, aquifers are isolated from the petroleum and hydraulic fracturing fluids by thick steel pipes (casing) that are cemented into the ground. When properly cemented, they form an effective barrier to fluids in the producing reservoir and prevent them from migrating up the hole, out of the borehole, and into an aquifer. Proper cementing also prevents fluids on the ground from migrating down the hole. One conceivable risk is that an improper cement job on the outside of the casing could permit frac fluids and oil and gas from the reservoir to travel up the outside of the casing (the annulus) and enter an aquifer through cracks in the cement. While that risk may exist, proper procedures by the well's operators and inspections by Division of Oil and Gas officials greatly reduce the chance of contaminating the aquifer. This risk is the same for conventional petroleum wells that are not hydraulically fractured.
Surface Contamination
Release of contaminants at the surface might occur while recovering injected flow-back fluids from a well. A recent study reported that the release of methane into the atmosphere is a significant problem, especially for shale-gas reservoirs, which have been popular exploration targets in recent years (Howarth and others, 2011). Release of carcinogens or other harmful toxins contained in hydraulic fracturing fluids is also reported in preliminary results from Colorado (McKenzie and others, 2012).
In many instances where hydraulic fracturing has been blamed for contaminating aquifers, the problem was actually caused by industrial accidents during conventional operations, for example, poor cementing of the well casing or a contaminant spill. Regardless of the setting, surface contamination is a potential risk for any petroleum well. One solution is to isolate the fracking fluid components and contain them at the surface where they can be either treated or removed.
Another possible risk of contamination occurs during the time when the fracturing fluids are mixed at the surface. Since fracture fluid components are contained in mobile tanks, and the movement of fluids are isolated in the tanks, extensive contamination on the ground surface is unlikely.
Thorough characterization of the background (pre-fracking) groundwater conditions and surface environmental conditions of an area must be available to make an objective and fair comparison of the water quality and surface environmental conditions before and after fracking. Rigorous sampling and analytical laboratory procedures must also be followed to assure the integrity of the results (NGWA, 2013; Saba, 2013).
Earthquakes and Hydraulic Fracturing
Concerns that hydraulic fracturing is linked to earthquakes is a lively topic in the popular media. To avoid any misunderstanding of the issue, it is important to recognize that the hydraulic fracturing process itself has never been associated with any serious or threatening seismic event. The only significant connection between fracking and seismic risk is indirect: large frac jobs can use lots of water, and one method of dealing with the recovered frac fluid has been to inject it into waste disposal wells where it is confined deep underground. If many petroleum wells in an area are hydraulically fractured, the volume of waste water that is disposed of in this way can be considerable. Although waste disposal wells are generally used with no negative consequences, we've known for more than 50 years that, in a small number of cases, deep injection can initiate quakes in the small to medium strength range (Healy and others, 1968; NRC, 2014). The quakes that do occur are relatively small, and injection is ceased whenever a well is tied to a seismic event.
Earthquakes initiated by human activities, including the injection or extraction of fluids from wells, are said to be the product of "induced seismicity." Both natural and induced earthquakes are initiated by sudden movements of massive blocks of underground rock that shift their positions when certain threshold pressure conditions are present. For the most part, movement of these blocks follow along the surfaces of previously existing faults and fractures. The sudden release of energy when the rock ruptures and moves is an earthquake. An excellent comprehensive review of induced seismicity (Ritzel, 2013) is available to the public (http://fullerfuture.files.wordpress.com/2013/12/frackingindustrializationandinducedearthquakes-12-2-13.pdf).
Most known earthquakes associated with injection or extraction of fluids from or into wells have M3 or lower magnitude (Nicholson and Wesson, 1990, Table 1), meaning that they can be sensed by seismometers, but are rarely perceived by people and pose little threat, if any, to humankind or to the environment (BESR, 2012; Ellsworth, 2013).
Waste Injection and Earthquakes
Waste disposal wells that are known to have induced earthquakes have been documented in different states, including Arkansas, Colorado, Kansas, New Mexico, New York, Ohio, Oklahoma, Pennsylvania, Texas, and Wyoming (Kerr, 2012; King, 2012). None have been documented in Indiana. Even though hydraulically fractured wells themselves are not known to cause damaging earthquakes, the induced seismicity of waste disposal wells should be addressed; many of these wells are drilled for the purpose of disposing the large volumes of waste water associated with hydraulic fracturing.
The reason that deep waste injection wells occasionally cause small to moderate earthquakes, while hydraulically fractured petroleum wells themselves do not, is tied to the different objectives and operational needs associated with each type of well. In a typical well undergoing hydraulic fracturing, the goal is to continue to inject water, sand, and chemicals under great pressure into petroleum-bearing strata until the injection pressure exceeds the rock's strength and fractures are created or expanded into the reservoir rock. At the end of the treatment, which usually lasts a few days, injection is discontinued, the pressure decreases, and fluid movement reverses direction under pressures similar to those present before the fracturing began. Oil, gas, and water in the reservoir move toward the borehole, and then up the pipe into a collection or treatment facility on the surface. Because the high injection pressure ceases to add stress to the rock column, the operation of the producing well is unlikely to trigger earthquakes.
In contrast, injection wells for waste disposal are meant to transport fluids away from the wellbore and into a reservoir where they will reside indefinitely. As long as the well continues to be used for injection, pressures will remain high and will drive waste fluids away from the borehole. Pressure may build as more fluids are squeezed into the disposal reservoir, which can reactivate movement along any nearby, preexisting faults, resulting in small- to medium-strength earthquakes (M1 to M3). So far, the vast majority of these injection-related earthquakes have been small and detectable only by seismometers. However, two well-documented cases—Rocky Mountain Arsenal, Colorado (1960s, M5.2) and Paradox Valley, Colorado (1990s, M4.3)—demonstrated that fluid waste injection could trigger earthquakes along fault zones where natural high pressures (or stresses) already existed (Horton, 2012).
Waste disposal wells are a commonly used means to dispose of hydraulic fracturing fluids. During oil and gas production, both naturally occurring waters and chemicals may be produced. These waste fluids are commonly disposed in injection wells. The risk of inducing earthquakes by disposing of waste fluids in deep wells is a serious and reasonable concern that deserves careful monitoring. Injection wells are a common means of disposing of all sorts of industrial wastes, including wastes unrelated to oil and gas activities. The National Research Council of the Academies (2014) assembled data from a number of studies to demonstrate that a strong relationship exists between the rate of injection and the number of earthquakes occurring in the injection/quake-affected area.
Conclusions
Questions about environment and health deserve careful study. In Indiana, hydraulic fracturing in vertical wells has been used extensively for about 60 years with no evident instances of aquifer contamination. The evidence that is now available does not suggest a compelling need to restrict or prohibit hydraulic fracturing before a more thorough scientific evaluation of the ramifications is completed. The Environmental Protection Agency is conducting an extensive evaluation of hydraulic fracturing in the Unit